- Home
- die casting vs sand casting
Differences Between Die Casting vs Sand Casting: Which is Better for Manufacturers?
Welcome to Neuland Metals Company, a leading manufacturer and supplier of high-quality metal casting products for a variety of industries. Our state-of-the-art facilities and expertise in both die casting and sand casting processes allow us to offer a wide range of customized OEM products to meet our customers' unique specifications.
When it comes to die casting vs sand casting, both methods have their own advantages. Die casting produces parts with a superior surface finish and dimensional accuracy, making it ideal for complex and detailed components. On the other hand, sand casting is a more cost-effective option for producing larger and heavier parts with a lower tooling cost.
At Neuland Metals Company, we understand the importance of choosing the right casting method for your project. Our team of experienced engineers and technicians can help you determine the best approach for your specific requirements, ensuring high-quality and cost-efficient solutions for your products.
Choose Neuland Metals Company for all your casting needs and experience excellence in every part produced.
Neuland Metals Company
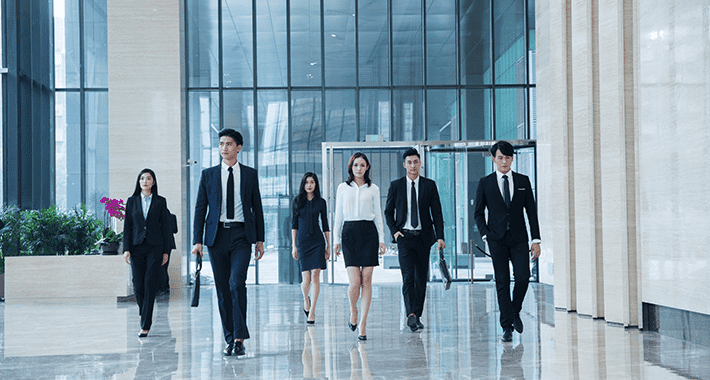
Company News
Related News
Engine Block Grey iron 250, GG25, EN-GJL-250 (EN-JL1040), FC250
Get high-quality grey iron engine blocks at our factory. Choose from GG25, EN-GJL-250, and FC250 grades. Durable and reliable. Order now!
Truck part Aluminum A356, A355.0, A360, A380, AlSi7Mg
High-quality aluminum truck parts including A356, A355.0, A360, A380, AlSi7Mg. Order direct from our factory for dependable performance and durability.
Green sand casting FCD400-15, FCD500-7, FCD600-3
Shop high-quality Green sand casting products like FCD400-15, FCD500-7, FCD600-3 at our factory. Durable and reliable metal castings for your needs.
Welding products Stainless steel, alloy steel, carbon steel. Ductile iron, grey iron
Introducing our top-quality welding products including stainless steel, alloy steel, carbon steel, ductile iron, and grey iron. As a factory, we ensure premium quality and durability.
Brass casting C86700, LG2, G1, G-cuSn5ZnPb, G-CuPb20Sn
Shop our high-quality brass casting products including C86700, LG2, G1, G-cuSn5ZnPb, G-CuPb20Sn. Factory-direct prices and fast shipping. Order now!
CNC machining parts Stainless steel, alloy steel, carbon steel
CNC Machining Parts: Stainless Steel, Alloy Steel, Carbon Steel. We are a factory specializing in high-quality metal components. Contact us for custom orders!
Motor fan shield A360, A380, AlSi7Mg, AlSi12, AlSi9Mg, ADC12
Get high-quality motor fan shields in A360, A380, AlSi7Mg, AlSi12, AlSi9Mg, ADC12 at our factory. Durable and reliable options for all your needs.
Valve parts ASTM 60-40-18, 65-45-12, 70-50-05, 80-55-06
High quality valve parts including ASTM 60-40-18, 65-45-12, 70-50-05, 80-55-06. Factory-direct prices. Buy now for reliable performance."
Braking pad for train Grey iron 250, GG25, EN-GJL-250 (EN-JL1040), FC250
Get reliable train braking pads made from high-quality Grey iron 250 at our factory. We specialize in GG25, EN-GJL-250, and FC250 iron products.
Stainless steel casting A380, AlSi7Mg, AlSi12, AlSi9Mg
Looking for high-quality {Stainless steel casting, A380, AlSi7Mg, AlSi12, AlSi9Mg} products? Our factory specializes in producing top-notch castings for various applications.
Gears Quenched and tempered steel, quenched steel
Introducing Gears, our quenched and tempered steel product line. Made with high-quality quenched steel, perfect for heavy-duty industrial use. Visit our factory today for top-notch products.
Fan for motor C86700, LG2, G1, G-cuSn5ZnPb, G-CuPb20Sn
Shop our quality fan for motor C86700, LG2, G1, G-cuSn5ZnPb, G-CuPb20Sn. As a factory, we offer durable and reliable products for all your motor needs.
CrNi alloy steel Chain Link
Shop our durable CrNi alloy steel chain link for reliable performance. Manufactured by our factory for superior quality and strength.
Auto parts GGG40, GGG40.3 GGG50,GGG60,GGG70
Buy high-quality GGG40, GGG40.3, GGG50, GGG60, GGG70 auto parts directly from the factory. Our products are durable and built to last.
Trailer hitch Stainless steel, alloy steel, carbon steel,Ductile iron
Stainless Steel Trailer Hitch - Quality alloy, carbon steel, and ductile iron products. Factory direct. Shop now for durable and reliable trailer hitches.
- Differences Between Die Casting vs Sand Casting: A Guide for Manufacturers
- Reviews
- Related Videos
Are you looking for high-quality and durable metal parts for your manufacturing needs? If so, you have come to the right place. Our company specializes in both die casting and sand casting processes to provide you with the perfect solution for your specific product requirements. Die casting is a process that involves injecting molten metal into a steel mold under high pressure, resulting in highly accurate and complex shapes with a smooth surface finish. This method is ideal for producing intricately designed parts with tight tolerances, making it suitable for a wide range of industries such as automotive, aerospace, and electronics. On the other hand, sand casting is a more traditional method that uses a pattern to create a cavity in sand, which is then filled with molten metal to form the desired shape. This process is versatile and cost-effective, making it suitable for producing large and heavy parts with a wide range of alloys. Whether you need precision parts with intricate designs or large and robust components, our die casting and sand casting capabilities have got you covered. With our advanced technology and skilled workforce, we are committed to delivering high-quality metal parts that meet your exact specifications and exceed your expectations. Contact us today to discuss your casting needs and let us provide you with the perfect solution for your next project.
I recently purchased a product that was made using die casting and I was blown away by its quality and precision. Die casting ensures that the final product has a smooth finish and is incredibly durable. The intricate designs and details were perfectly captured, giving the product a high-end look and feel. On the other hand, products made using sand casting tend to have a rougher finish and may not be as precise in terms of intricate designs. Overall, I am extremely satisfied with the die-cast product and would highly recommend it for anyone looking for high-quality and precise products.
I recently compared die casting and sand casting for a small metal part, and found that die casting offered superior results. The die casting process yielded a more precise and consistent product, with smooth surface finishes and intricate details. In contrast, sand casting produced a rougher surface and required more post-processing to achieve the desired quality. Additionally, die casting allowed for a faster production cycle, reducing lead times and overall costs. Overall, I highly recommend die casting for high-quality, complex metal parts over sand casting.
Contact us
Please feel free to give your inquiry in the form below We will reply you in 24 hours