Top Aluminum Die Cast Supplier in China for Quality Products
By:Admin
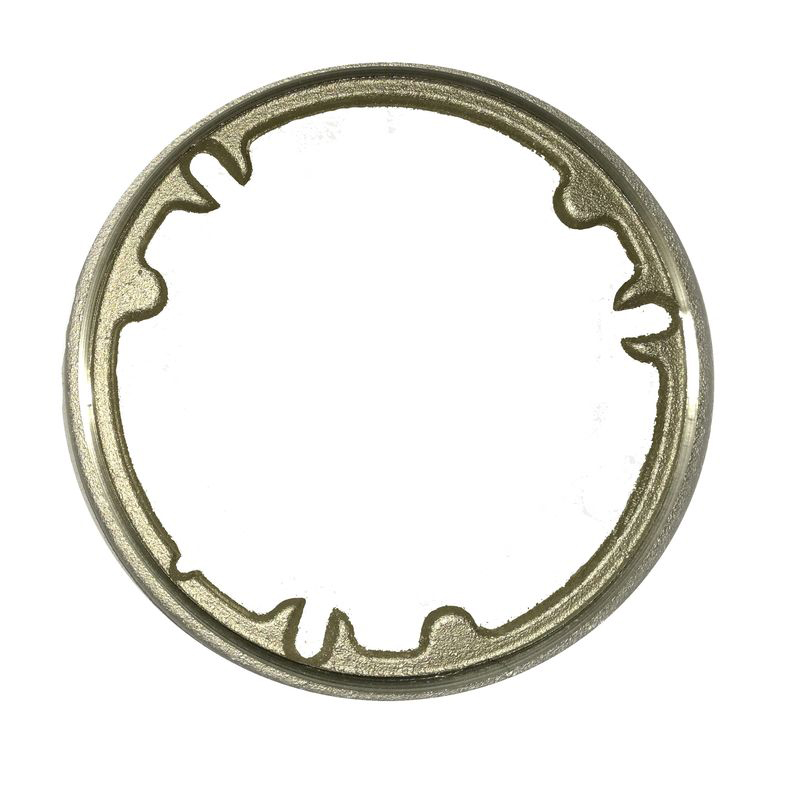
China - As the demand for high-quality aluminum die cast products continues to rise, one of China's leading aluminum die cast suppliers is expanding its operations to meet the needs of their growing customer base. With a commitment to providing top-notch die cast products and exceptional customer service, this supplier is poised to become a go-to source for businesses around the world.
With a focus on meeting the highest quality standards, this supplier has established a strong reputation for delivering precision die cast products that are durable, reliable, and cost-effective. By leveraging state-of-the-art technology and innovative manufacturing processes, they are able to produce a wide range of aluminum die cast products that meet the specific needs and requirements of their customers.
The company's dedication to excellence doesn't stop at the production line - they also place a strong emphasis on providing exceptional customer service. From the initial inquiry to the final delivery of the products, their team of experts is committed to ensuring a seamless and satisfying experience for each and every customer.
In response to the growing demand for their products, this supplier has recently expanded their manufacturing facilities to increase their production capacity and improve efficiency. By investing in new equipment and technology, they are able to meet the needs of their customers more effectively and deliver products on time, every time.
In addition to expanding their manufacturing capabilities, this supplier has also increased their workforce to accommodate the growing demand for their products. By hiring skilled workers and professionals, they are able to maintain their high standards of quality and continue to provide exceptional products and services to their customers.
This expansion comes at a time when the demand for aluminum die cast products is on the rise across a wide range of industries. From automotive and aerospace to electronics and consumer goods, businesses are turning to aluminum die cast products for their lightweight, durable, and cost-effective properties. With this in mind, this supplier is well-positioned to meet the needs of businesses around the world.
By expanding their operations, this supplier is not only able to meet the current demand for aluminum die cast products but also to position themselves to take advantage of future growth in the industry. By staying ahead of the curve and investing in their capabilities, they are ensuring that they can continue to deliver exceptional products and services to their customers for years to come.
As they continue to expand their operations, this supplier remains committed to their core values of quality, innovation, and customer satisfaction. By staying true to these values, they are confident that they can continue to be a trusted and reliable partner for businesses in need of high-quality aluminum die cast products.
With their expanded capabilities and commitment to excellence, this China aluminum die cast supplier is well-positioned to meet the growing demand for their products and to continue to be a leader in the industry. Businesses looking for top-notch die cast products can turn to this supplier with confidence, knowing that they will receive the highest quality products and the best customer service in the industry.
Company News & Blog
Ultimate Guide to Sand Casting: Everything You Need to Know
Sand Casting is a widely used method for producing metal parts. It involves pouring molten metal into a sand mold, which is then allowed to cool and solidify, creating the desired shape. This process is particularly well-suited for large and heavy metal parts, as well as complex and intricate designs.One company that specializes in sand casting is {}. With over 30 years of experience in the industry, {} has established itself as a leader in the field of metal casting. The company's state-of-the-art facilities and highly skilled workforce enable it to produce high-quality sand castings for a wide range of industries, including automotive, aerospace, and machinery manufacturing.The sand casting process begins with the creation of a mold made from specially formulated sand. The mold is formed by compacting the sand around a pattern, which is then removed to leave a cavity in the shape of the desired part. Molten metal is then poured into the mold, filling the cavity and taking on its shape as it cools and solidifies. Once the metal has cooled, the sand mold is broken away to reveal the finished casting.{}'s sand casting capabilities are extensive, allowing the company to produce parts in a variety of metals, including aluminum, iron, and steel. This versatility makes sand casting an attractive option for a wide range of applications, from small and intricate components to large and heavy-duty parts. In addition, the company's advanced equipment and technology ensure that each casting meets the highest standards of quality and accuracy.One of the main advantages of sand casting is its ability to produce complex and detailed parts with relatively low tooling costs. This makes it an economical choice for small to medium production runs, as well as for prototype and custom parts. At the same time, the versatility of sand casting allows for the production of large and heavy parts that would be impractical or cost-prohibitive to produce using other methods.In addition to its technical capabilities, {}'s commitment to quality and customer satisfaction sets it apart in the industry. The company's stringent quality control measures ensure that each casting meets the required specifications and standards, while its dedicated team of engineers and technicians work closely with clients to understand their needs and deliver custom solutions. This collaborative approach, combined with the company's expertise and capabilities, has earned {} a reputation for excellence and reliability in the field of sand casting.Looking ahead, {} continues to invest in its facilities and technology to further enhance its sand casting capabilities. The company's ongoing commitment to innovation and improvement ensures that it remains at the forefront of the industry, delivering top-quality castings that meet the evolving needs of its customers.In conclusion, sand casting is a versatile and cost-effective method for producing metal parts, and {}'s expertise and capabilities in this area make it a trusted partner for a wide range of industries. With its advanced facilities, skilled workforce, and dedication to quality, the company is well-positioned to continue meeting the diverse casting needs of its customers for years to come.
Quality Die Casting Services in China: What You Need to Know
Die casting is a precision manufacturing process used to create metal parts by injecting molten metal into a steel mold or die, under high pressure. It is a highly efficient and cost-effective method for producing complex, high-quality parts with excellent surface finishes. As a leading die casting company in China, [Company Name] has been at the forefront of the industry, providing innovative solutions and unparalleled expertise in die casting production.With a history of over 20 years, [Company Name] has built a strong reputation for delivering high-quality die casting products to a wide range of industries including automotive, aerospace, electronics, and more. The company has a state-of-the-art manufacturing facility equipped with advanced die casting machines, CNC machining centers, and quality control systems to ensure the highest level of precision and consistency in their products.Recently, [Company Name] has been making waves in the die casting industry by introducing new cutting-edge technology and expanding their capabilities to meet the evolving needs of their customers. One of the key advancements they have made is in the area of alloy development and casting processes. By working closely with material suppliers and conducting extensive research and development, [Company Name] has been able to expand their range of die casting alloys to offer customers a wider selection of materials with superior performance characteristics.In addition, the company has also invested in the latest die casting machinery to increase their production capacity and improve efficiency. By incorporating advanced automation and robotics in their manufacturing processes, [Company Name] has been able to significantly reduce lead times and production costs, while maintaining the highest level of product quality and consistency.Furthermore, [Company Name] has been dedicated to implementing sustainable and environmentally-friendly practices in their die casting operations. They have adopted energy-efficient technologies and have implemented recycling and waste reduction programs to minimize their environmental footprint. This commitment to sustainability has resonated well with their customers and has positioned [Company Name] as a responsible and forward-thinking die casting partner.As part of their ongoing efforts to provide comprehensive die casting solutions, [Company Name] also offers value-added services such as precision machining, surface finishing, and assembly. This allows customers to streamline their supply chain and reduce costs by consolidating their manufacturing needs with a trusted and reliable partner.With a strong focus on customer satisfaction, [Company Name] places a high priority on maintaining open and transparent communication with their clients throughout the die casting process. Their team of experienced engineers and production experts work closely with customers from the initial design phase through to final production, providing technical support and guidance to ensure that the final product meets or exceeds expectations.Looking ahead, [Company Name] is committed to staying at the forefront of the die casting industry by continuing to invest in technology, infrastructure, and talent to further enhance their capabilities and provide superior die casting solutions to their customers. With an unwavering dedication to quality, innovation, and customer satisfaction, [Company Name] is positioned for continued success and growth in the global die casting market.
Durable epoxy coated cast iron pipes: a sustainable plumbing solution
Epoxy Coated Cast Iron Pipe - The Next Evolution in Plumbing TechnologyIn the modern world, the need for reliable and durable plumbing solutions is more important than ever before. As cities grow and infrastructure is put to the test, it is crucial for plumbing systems to be able to withstand the demands of daily use. This is where epoxy coated cast iron pipes come into play, offering a revolutionary new solution that provides long-lasting durability and reliability.One company that is leading the way in the development and production of epoxy coated cast iron pipes is {Company Name}. With a strong commitment to innovation and quality, {Company Name} has quickly become a trusted leader in the industry, providing the latest in plumbing technology to cities and communities around the world.{Company Name} has a long history of providing high-quality plumbing solutions to their customers. With a focus on research and development, the company has been able to stay at the forefront of the industry, constantly pushing the boundaries of what is possible in plumbing technology. This commitment to innovation has led to the development of their epoxy coated cast iron pipe, a product that is quickly gaining attention for its superior performance and durability.The epoxy coated cast iron pipe offered by {Company Name} is a game changer in the world of plumbing. By combining the strength and reliability of cast iron with the corrosion resistance of epoxy coating, this pipe is able to provide a level of durability that is unmatched by traditional plumbing materials. This means that cities and communities can rely on these pipes to provide long-term, dependable service, even in the most demanding of environments.One of the key benefits of epoxy coated cast iron pipes is their resistance to corrosion. Traditional cast iron pipes are susceptible to rust and corrosion over time, leading to a decrease in performance and an increase in maintenance costs. However, with the addition of an epoxy coating, {Company Name}'s pipes are able to resist the effects of corrosion, providing a longer service life and reducing the need for costly repairs and replacements.In addition to their durability, {Company Name}'s epoxy coated cast iron pipes are also designed with ease of installation in mind. The lightweight nature of these pipes makes them easier to handle and install, reducing the time and labor required for plumbing projects. This not only makes them more cost effective, but also ensures that installations can be completed more efficiently, minimizing disruption to local communities.{Company Name} is dedicated to providing the highest quality products and services to their customers. This commitment extends beyond the production of their epoxy coated cast iron pipes, as the company also offers comprehensive support and expertise to assist with the planning and installation of plumbing projects. This level of service ensures that customers are able to make the most of {Company Name}'s innovative plumbing solutions, leading to successful and reliable results.As cities and communities continue to grow and develop, the need for durable and reliable plumbing solutions will only become more important. With their epoxy coated cast iron pipes, {Company Name} is leading the way in providing a solution that meets the demands of modern plumbing needs. With their commitment to innovation and quality, it is clear that {Company Name} is a trusted partner for cities and communities around the world, providing the latest in plumbing technology to ensure a reliable and sustainable future.
Cast Iron Elbow Fitting: A Guide to China's Latest Product
China Cast Iron Elbow Fitting Leads the Industry with Superior Quality and InnovationChina has long been known for its exceptional craftsmanship and innovative technology in the manufacturing industry. One company that is leading the charge in this sector is [Company Name]. Specializing in the production of cast iron elbow fittings, the company has established itself as a key player in the global market.With a history dating back to [Year], [Company Name] has been at the forefront of the industry, delivering high-quality products and exceeding customer expectations. The company's dedication to innovation and excellence has earned it a strong reputation in both domestic and international markets. Leveraging state-of-the-art technology and a team of skilled professionals, [Company Name] has set new benchmarks for quality and reliability in the industry.The cast iron elbow fittings produced by [Company Name] are widely recognized for their superior performance and durability. Built to withstand the most demanding applications, these fittings are highly sought after in various sectors, including plumbing, construction, and industrial manufacturing. In addition to their exceptional strength, [Company Name]'s fittings also boast a sleek and elegant design, making them a preferred choice for architects and designers.One of the key factors that sets [Company Name] apart from its competitors is its commitment to sustainability and environmental responsibility. The company prioritizes eco-friendly practices in its manufacturing processes, ensuring that its products have minimal impact on the environment. This dedication to sustainability has not only earned [Company Name] the trust of its customers but has also positioned it as a pioneer in green manufacturing practices.In a recent interview, [Company Name]'s CEO, [CEO Name], highlighted the company's unwavering dedication to innovation and customer satisfaction. "At [Company Name], we are committed to pushing the boundaries of what is possible in the manufacturing industry. Our goal is to not only meet the needs of our customers but to exceed their expectations at every turn. Whether it's through our cutting-edge technology or our relentless pursuit of excellence, we are constantly striving to set new standards for quality and innovation."[Company Name] has also made significant investments in research and development, continually seeking new ways to improve its products and processes. By staying ahead of the curve and embracing the latest trends in the industry, the company has solidified its position as a trendsetter and trailblazer.The global demand for cast iron elbow fittings is on the rise, and [Company Name] is well-equipped to meet this demand with its extensive production capabilities. The company's state-of-the-art manufacturing facilities are designed to optimize efficiency and productivity, enabling it to deliver large quantities of high-quality fittings to customers around the world. With a strong focus on customer satisfaction and a robust distribution network, [Company Name] has successfully expanded its reach to serve clients in various continents.Looking ahead, [Company Name] remains committed to its core values of integrity, quality, and innovation. The company is poised to continue its growth trajectory and further elevate its standing in the global market. By staying true to its mission of delivering excellence in every aspect of its operations, [Company Name] is set to shape the future of the industry and cement its status as a leading provider of cast iron elbow fittings.In conclusion, [Company Name] has established itself as a true industry leader, setting new standards for quality and innovation in the manufacturing of cast iron elbow fittings. With its unwavering commitment to excellence and sustainability, the company has not only earned the trust of its customers but has also positioned itself as a driving force in the market. As the demand for high-quality fittings continues to grow, [Company Name] is well-prepared to meet this demand and lead the industry into a new era of innovation and success.
Top Benefits of Stainless Metal Stamping in Manufacturing Industry
Stainless Metal Stamping Technology Revolutionizes Manufacturing ProcessIn the world of manufacturing, the process of metal stamping has long been a crucial component in the production of various metal parts and components. However, with the emergence of advanced technologies, it has become increasingly important for companies to stay ahead of the curve and embrace innovative techniques that can revolutionize the manufacturing process. This is where the introduction of stainless metal stamping technology by {Company Name} has changed the game and set a new standard for efficiency and quality in the industry.{Company Name} is a leading manufacturing company that has been at the forefront of innovation in metal stamping and fabrication for decades. Established in {year}, the company has built a solid reputation for its commitment to excellence, precision, and customer satisfaction. Over the years, {Company Name} has continuously invested in cutting-edge technologies and state-of-the-art equipment to stay ahead of the competition and meet the evolving needs of its clients across various industries.The introduction of stainless metal stamping technology is the latest milestone for {Company Name}, representing a significant advancement in its manufacturing capabilities. This new technology allows for the precise and efficient production of metal parts and components using stainless steel, a material known for its durability, corrosion resistance, and aesthetic appeal. By leveraging this advanced stamping technology, {Company Name} is able to meet the growing demand for high-quality stainless steel components in industries such as automotive, aerospace, medical, and more.One of the key advantages of stainless metal stamping is its ability to produce complex and intricate parts with unparalleled precision and consistency. This means that {Company Name} can now manufacture a wide range of stainless steel components, including brackets, housings, enclosures, and other specialized parts, with greater efficiency and cost-effectiveness. This not only benefits the company's bottom line but also translates to a competitive edge for its clients who rely on the superior quality of these components in their own products and operations.Furthermore, stainless metal stamping technology enables {Company Name} to offer customizable solutions to its customers, tailored to their specific design requirements and production needs. Whether it's a small batch of custom stainless steel parts or a large-scale production run, the flexibility of this technology allows {Company Name} to deliver precision-engineered components with a quick turnaround time, ultimately providing its clients with a competitive advantage in their respective markets.In addition to its technical capabilities, {Company Name} has also invested in a team of highly skilled engineers, technicians, and quality control specialists who are dedicated to upholding the highest standards of excellence in the manufacturing process. This commitment to quality assurance, coupled with the advanced stainless metal stamping technology, ensures that every component produced by {Company Name} meets the most stringent industry standards and customer specifications.As {Company Name} continues to lead the way in the evolution of metal stamping technology, it remains dedicated to its core values of innovation, precision, and customer satisfaction. By integrating stainless metal stamping into its manufacturing capabilities, {Company Name} is not only raising the bar for quality and efficiency in the industry but also reinforcing its position as a trusted partner for businesses seeking top-notch metal fabrication solutions.In conclusion, the introduction of stainless metal stamping technology by {Company Name} marks a significant milestone in the manufacturing industry. As the company continues to push the boundaries of innovation and excellence, it is poised to make a lasting impact on the way stainless steel components are produced and utilized across various sectors. With its unwavering commitment to quality and customer-centric approach, {Company Name} is set to revolutionize the manufacturing process and set a new standard for precision and efficiency in metal stamping.
High-Quality Aluminum Investment Casting: Everything You Need to Know
Aluminum Investment Casting: The Future of ManufacturingInvestment casting, also known as lost-wax casting, is a manufacturing process that has been used for centuries to create intricate and complex metal components. It involves the creation of a wax model, which is then coated in a ceramic shell and melted out, leaving a hollow space into which molten metal is poured. This process allows for the production of highly detailed and precise parts, making it a popular choice in industries such as aerospace, automotive, and defense.One company that has been at the forefront of aluminum investment casting is {}. With over 50 years of experience in the industry, {} has established itself as a leading supplier of high-quality aluminum castings to a wide range of industries. Their commitment to innovation and excellence has made them a trusted partner for companies looking for reliable and high-performance components.One of the key advantages of aluminum investment casting is its ability to create complex geometries with tight tolerances. This makes it an ideal choice for applications that require lightweight, yet durable components. The process also allows for the production of thin-walled sections and intricate details that would be difficult or impossible to achieve using other manufacturing methods. This flexibility has made aluminum investment casting a popular choice in industries such as aerospace, where weight and performance are critical factors.In addition to its versatility, aluminum investment casting offers a number of other benefits. The process produces parts with excellent surface finishes and minimal machining allowances, reducing the need for secondary operations and resulting in cost savings. Aluminum also has a high strength-to-weight ratio, making it an ideal material for applications where weight reduction is important. Furthermore, aluminum is highly corrosion-resistant, making it suitable for use in a wide range of environments.{} has extensive experience in working with a variety of aluminum alloys, allowing them to tailor their process to meet the specific requirements of each application. Their team of skilled engineers and technicians works closely with customers to understand their needs and develop solutions that deliver the performance and quality they require. From initial design and prototyping through to full-scale production, {} provides a comprehensive range of services to ensure that their customers receive the best possible outcomes.With an unwavering commitment to quality, {} has invested in state-of-the-art equipment and advanced technologies to ensure that their aluminum investment casting process meets the highest standards. Their modern facilities and rigorous quality control measures ensure that each part they produce consistently meets or exceeds customer expectations. By leveraging the latest advancements in materials and process automation, {} is able to deliver cost-effective solutions without compromising on quality.As the demand for lightweight, high-performance components continues to grow across a wide range of industries, aluminum investment casting is poised to play an increasingly important role in the future of manufacturing. With its ability to produce complex parts with minimal machining and excellent mechanical properties, it offers a compelling solution for companies looking to enhance their products and stay ahead of the competition. As a leader in the field, {} is well-positioned to meet this growing demand and continue to drive innovation in aluminum investment casting.In conclusion, aluminum investment casting is a highly versatile and cost-effective manufacturing process that offers a wide range of benefits. With its ability to produce complex geometries, thin-walled sections, and high-quality surface finishes, it is well-suited to a variety of applications across different industries. As a leading provider of aluminum investment casting solutions, {} is committed to delivering exceptional value to its customers and driving forward the future of manufacturing.
High-quality Custom Machining and Forging Services for Your Business
Custom machining and forging techniques have long been essential in the manufacturing industry, providing companies with the ability to create complex and unique parts for a wide range of applications. One company at the forefront of this industry is {}, which has established itself as a leader in providing high-quality custom machining and forging solutions.With a strong emphasis on quality and precision, {} has become a trusted partner for companies in various industries, including aerospace, automotive, defense, and more. The company's commitment to excellence can be seen in its state-of-the-art facilities, advanced technology, and highly skilled team of engineers and technicians.{} offers a comprehensive range of custom machining and forging services, including CNC machining, turning, milling, grinding, and more. This allows the company to meet the diverse needs of its clients, providing them with custom parts that are tailored to their specific requirements. Whether it's a one-of-a-kind prototype or a large production run, {} has the capability to deliver high-quality parts on time and within budget.In addition to its custom machining capabilities, {} also specializes in forging, which allows the company to create parts with exceptional strength and durability. The company utilizes a variety of forging techniques, including open-die, closed-die, and ring rolling, to produce high-quality parts that meet the most demanding requirements. Whether it's for a critical aerospace component or a heavy-duty industrial application, {} has the expertise and resources to deliver superior forged parts.One of the key strengths of {} is its ability to work closely with clients to understand their unique needs and develop tailored solutions. The company's team of engineers and technicians are dedicated to providing the highest level of service and support, working collaboratively with clients to ensure that their specific requirements are met. This customer-centric approach has earned {} a strong reputation in the industry, and has led to long-lasting partnerships with many of its clients.As a company that is committed to staying at the forefront of technological advancements, {} continually invests in the latest equipment and technology. This allows the company to maintain its competitive edge and provide clients with the best possible solutions for their custom machining and forging needs. By staying ahead of the curve, {} is able to offer innovative solutions that meet the evolving demands of the manufacturing industry.In addition to its focus on quality and innovation, {} is also dedicated to maintaining the highest standards of safety and environmental responsibility. The company adheres to strict safety protocols in its facilities, ensuring that its team members are able to work in a safe and secure environment. Furthermore, {} is committed to minimizing its environmental footprint and operates in a sustainable manner, utilizing energy-efficient processes and minimizing waste wherever possible.With its dedication to quality, innovation, and customer satisfaction, {} continues to be a leader in the custom machining and forging industry. The company's ability to provide high-quality, customized solutions for a wide range of applications has made it a trusted partner for companies across various industries. As {} continues to grow and expand its capabilities, it is well-positioned to meet the evolving needs of the manufacturing industry and continue to provide exceptional custom machining and forging solutions.
Understanding the Die Forging Process: A Comprehensive Guide
Die Forging, also known as drop forging, is a metal shaping process in which a heated metal bar is placed in a die and then struck by a hammer or press to form it into the desired shape. This process is commonly used in the manufacturing of automotive parts, aerospace components, and heavy machinery.In recent news, a leading company in the manufacturing industry, has announced an expansion of their die forging capabilities. With over years of experience, the company has established themselves as a trusted provider of high-quality forged components for a wide range of industries. The expansion of their die forging capabilities is a strategic move to meet the growing demand for forged components in the global market.The company has invested in state-of-the-art die forging equipment to enhance their production capabilities. This investment includes the acquisition of advanced hammers and presses that are capable of exerting immense force to shape metal bars into complex and precise components. Additionally, they have also expanded their workforce with highly skilled die forging experts to ensure the highest level of quality and precision in their production process.With this expansion, the company is poised to offer a wider range of die forged components to their clients. These components can range from simple shapes to intricate designs that require a high degree of precision. By leveraging their advanced die forging capabilities, they are able to produce components that meet the strictest tolerances and quality standards.Furthermore, the company’s die forging process is supported by their in-house metallurgical laboratory. This laboratory is equipped with the latest technology for metal analysis and testing, ensuring that the forged components meet the required material properties and performance standards. This commitment to quality control sets the company apart as a reliable supplier of die forged components for critical applications.The expansion of die forging capabilities also aligns with the company’s commitment to sustainability. By utilizing the die forging process, they are able to minimize material waste and achieve higher material utilization compared to other metal shaping processes. Additionally, the high strength and durability of die forged components contribute to the longevity and reliability of the end products, further reducing the environmental impact of manufacturing.The company’s die forging capabilities are not limited to a specific industry. They have the flexibility to produce components for automotive, aerospace, construction, and various other sectors. This versatility enables them to cater to diverse market needs and offer customized solutions for specific applications.In conclusion, the expansion of die forging capabilities by the company represents a significant milestone in their commitment to providing high-quality forged components to industries worldwide. With their investment in advanced equipment, skilled workforce, and focus on quality control, they are well-positioned to meet the evolving needs of the market. The company’s die forging process not only enables them to produce components with exceptional precision and strength, but also demonstrates their dedication to sustainability in manufacturing practices. As they continue to expand their capabilities, they are poised to solidify their reputation as a preferred supplier of die forged components for a wide range of applications.
Cold extrusion forging: an overview of metal forging methods and products
Cold Extrusion Forging: A Revolutionary Method in Metal ForgingForging is a manufacturing process that shapes metal using compressive forces. There are several methods of forging, each with its own advantages and disadvantages. One of the most innovative methods of forging is cold extrusion forging, which offers several benefits over traditional forging methods.Cold extrusion forging is a process that involves shaping metal at room temperature using compressive forces. This method allows for precise control over the shape and dimensions of the forged part, as well as the ability to create complex geometries. Additionally, cold extrusion forging is a cost-effective and efficient process, making it an ideal choice for a wide range of metal forging applications.There are several types of forging methods, including open-die forging, closed-die forging, and seamless rolled ring forging. Each method has its own unique advantages and is suitable for different types of metal forging products. Open-die forging, for example, is commonly used to produce large, simple-shaped parts, while closed-die forging is ideal for producing more complex, intricate parts. Seamless rolled ring forging, on the other hand, is used to create seamless, ring-shaped parts with the desired properties.Metal forging products produced using cold extrusion forging can be found in a wide range of industries, including automotive, aerospace, and construction. These products include shafts, gears, pistons, and various other components that require high strength and precise dimensions. The ability to produce these parts with tight tolerances and minimal waste makes cold extrusion forging an attractive option for manufacturers seeking to improve their production processes.One company that has embraced cold extrusion forging is {Company}. Founded in 1990, {Company} has established itself as a leading manufacturer of metal forging products using state-of-the-art technologies. The company's commitment to innovation and excellence has led to the development of advanced forging processes, including cold extrusion forging.{Company} specializes in the production of a wide range of forged products, including automotive components, industrial machinery parts, and aerospace components. The company's cold extrusion forging capabilities allow it to produce high-quality, precision-engineered parts that meet the most demanding specifications. By leveraging this advanced forging method, {Company} has been able to deliver superior products to its customers while maintaining a competitive edge in the industry.In addition to cold extrusion forging, {Company} also offers other forging methods, such as open-die forging and seamless rolled ring forging, to meet the diverse needs of its customers. With a strong focus on quality, reliability, and customer satisfaction, {Company} has built a reputation for excellence in the metal forging industry.As the demand for high-quality, precision-engineered metal forging products continues to grow, the adoption of advanced forging methods such as cold extrusion forging is expected to increase. Manufacturers seeking to improve the quality and efficiency of their production processes can benefit significantly from incorporating cold extrusion forging into their operations.In conclusion, cold extrusion forging is a revolutionary method in metal forging that offers several benefits over traditional forging methods. With its ability to produce precise, complex parts at room temperature, cold extrusion forging is a cost-effective and efficient solution for a wide range of metal forging applications. Companies like {Company} are leading the way in leveraging this advanced forging method to deliver superior products to their customers and maintain a competitive edge in the industry. As the industry continues to evolve, cold extrusion forging is poised to play a crucial role in shaping the future of metal forging.
Top Hot Forging Factories in China: Latest News and Updates
China Hot Forging Factories Improve Efficiency and Quality to Meet Growing DemandChina has long been known for its manufacturing prowess, and hot forging is no exception. Hot forging is a process used to shape metal by heating it in a furnace and then pressing it into a die to create the desired shape. This process is widely used in the automotive, aerospace, and construction industries, among others, and demand for hot forged parts is on the rise. In response to this increased demand, hot forging factories in China are working to improve their efficiency and quality to meet the needs of their customers.One such hot forging factory in China is {company name}, a leading manufacturer in the industry. With over 20 years of experience, {company name} has established a strong reputation for producing high-quality hot forged parts for a wide range of applications. The company has a state-of-the-art facility with advanced equipment and a team of skilled engineers and technicians who are dedicated to delivering top-notch products to their customers.In order to keep up with the growing demand for hot forged parts, {company name} has been working to improve its operational efficiency and enhance the quality of its products. One of the key initiatives the company has implemented is the adoption of advanced manufacturing technologies. By leveraging the latest equipment and software, {company name} has been able to streamline its production processes and reduce lead times, allowing them to deliver parts to their customers more quickly and efficiently.Additionally, {company name} has made significant investments in quality control and assurance. The company understands the importance of producing parts that meet the highest standards, and they have implemented rigorous quality control measures to ensure that every product that leaves their facility is of the utmost quality. By doing so, {company name} has been able to build trust and confidence with their customers, who rely on them to deliver parts that are reliable and durable.Another area of focus for {company name} has been on sustainability and environmental responsibility. The company has implemented eco-friendly practices in its manufacturing processes, such as recycling materials and reducing waste. By doing so, {company name} is not only reducing its environmental impact but also improving its operational efficiency and reducing costs.The efforts of {company name} and other hot forging factories in China to improve efficiency and quality are helping to meet the growing demand for hot forged parts. With their commitment to delivering top-notch products, these companies are playing a crucial role in supporting various industries, including automotive, aerospace, and construction. As the demand for hot forged parts continues to grow, these factories are poised to play an even more significant role in the global manufacturing landscape.In conclusion, hot forging factories in China, such as {company name}, are working tirelessly to enhance their operational efficiency and improve the quality of their products. By investing in advanced technologies, implementing stringent quality control measures, and prioritizing sustainability, these factories are meeting the growing demand for hot forged parts and supporting various industries around the world. As they continue to innovate and improve, these factories are well-positioned to remain leaders in the hot forging industry for years to come.