High-quality aluminum alloy die casting available for various industries
By:Admin
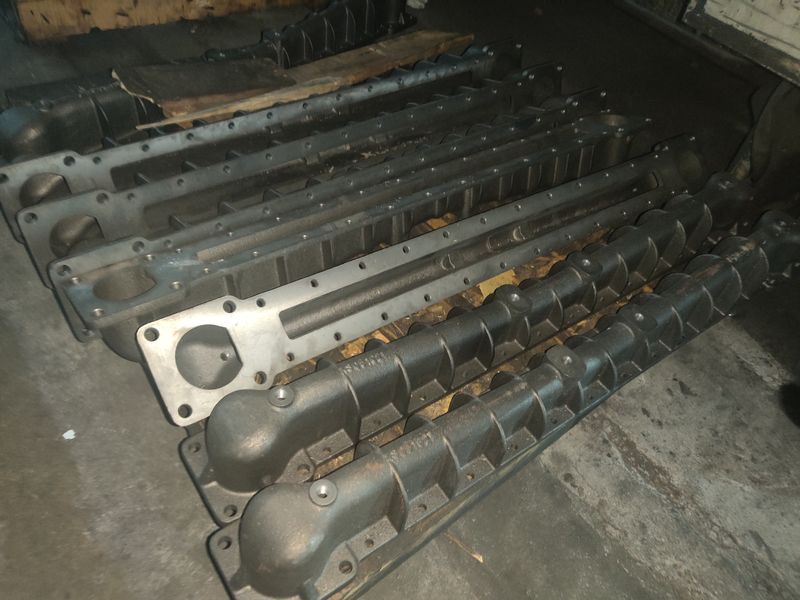
XYZ is a leading provider of innovative manufacturing solutions, pioneering advancements in the industry by integrating cutting-edge technology with precision engineering. With a commitment to excellence and a focus on continuous improvement, XYZ has solidified its position as a trusted partner for a wide range of industries, including automotive, aerospace, electronics, and more. Through a relentless pursuit of innovation, XYZ has recently introduced aluminum alloy die casting to its extensive list of capabilities, revolutionizing the manufacturing landscape and setting new standards for efficiency and quality.
Aluminum alloy die casting is a highly versatile process that allows for the production of complex, intricate parts with high dimensional accuracy. By utilizing aluminum alloy, which offers exceptional strength-to-weight ratio and excellent corrosion resistance, XYZ is able to deliver components that meet the most stringent performance requirements while maintaining cost-effectiveness. This capability is particularly beneficial for industries such as automotive and aerospace, where lightweight, durable parts are in high demand.
The introduction of aluminum alloy die casting at XYZ's state-of-the-art facility has been a game-changer for its clients, as it provides a one-stop solution for their manufacturing needs. With the ability to handle everything from design and prototyping to full-scale production, XYZ has significantly streamlined the production process, reducing lead times and costs for its customers. Coupled with its advanced quality control systems, XYZ ensures that every part produced through aluminum alloy die casting meets the highest standards for performance and reliability.
Moreover, XYZ's expertise in aluminum alloy die casting extends beyond just the manufacturing process. With a team of highly skilled engineers and technicians, XYZ offers comprehensive design for manufacturability (DFM) services, collaborating closely with its clients to optimize the design of their parts for the die casting process. This proactive approach not only results in better-quality parts but also maximizes production efficiency, ultimately providing a competitive advantage for its clients in their respective markets.
In addition to its technical capabilities, XYZ is also committed to sustainability and environmentally friendly practices. Aluminum alloy die casting aligns with XYZ's green initiatives, as it allows for the efficient use of materials and energy, minimizing waste and reducing the environmental footprint of the manufacturing process. By offering a sustainable manufacturing solution, XYZ is not only meeting the needs of its clients but also contributing to a more sustainable future for the industry as a whole.
Furthermore, XYZ's dedication to continuous improvement is exemplified by its ongoing investment in research and development. The company is constantly exploring new alloys, materials, and process innovations to further enhance its capabilities and stay at the forefront of technological advancements. This commitment to innovation ensures that XYZ remains a strategic partner for its clients, providing them with the most advanced manufacturing solutions to address their evolving needs and challenges.
As XYZ continues to push the boundaries of what is possible in manufacturing, the introduction of aluminum alloy die casting stands as a testament to the company's unwavering commitment to excellence and innovation. By combining its technical expertise, advanced capabilities, and a relentless pursuit of improvement, XYZ has set a new standard for the industry and solidified its position as a trusted leader in the manufacturing landscape. With aluminum alloy die casting, XYZ is not just revolutionizing manufacturing – it is shaping the future of the industry.
Company News & Blog
Cold Forging Process: Materials, Benefits, and Applications Explained
Steel Cold Forging is a process that has been gaining a lot of attention in the manufacturing industry in recent years. This innovative technique allows for the creation of complex and high-strength metal components with excellent surface finishes. With the demand for precision-engineered parts on the rise, {Company Name} has positioned itself as a leading provider of steel cold forging services, offering a wide range of solutions for various industries including automotive, aerospace, and electronics.{Company Name} is a renowned manufacturer with a strong track record of delivering top-quality components to its customers. The company’s state-of-the-art facilities and advanced technology enable it to produce complex parts with exceptional precision and efficiency. With a team of highly skilled engineers and technicians, {Company Name} is capable of providing custom cold forging solutions to meet the unique requirements of its clients.One of the key advantages of steel cold forging is its ability to produce parts with superior mechanical properties. By subjecting the metal to high compressive forces at room temperature, the process allows for greater control over the material’s grain structure, resulting in components with enhanced strength and durability. This makes steel cold forging a preferred choice for applications where reliability and performance are critical.{Company Name} specializes in cold forging a wide range of steel alloys, including carbon steel, stainless steel, and alloy steel. The company’s expertise in working with different materials allows it to offer comprehensive solutions for a diverse set of applications. Whether it’s producing intricate automotive components or critical aerospace parts, {Company Name} has the capability to deliver high-quality forged parts with tight tolerances and consistent quality.In addition to its cold forging capabilities, {Company Name} also provides a range of secondary processes such as heat treatment, machining, and surface finishing. This integrated approach allows the company to offer a one-stop solution, reducing the lead time and cost for its customers. With a focus on continuous improvement and innovation, {Company Name} strives to stay ahead of the curve in the rapidly evolving manufacturing landscape.The automotive industry is one of the key sectors that benefit significantly from steel cold forging. With the increasing demand for lightweight and fuel-efficient vehicles, automakers are constantly seeking ways to improve the performance of their vehicles while reducing production costs. Steel cold forging offers an ideal solution for producing lightweight yet durable components such as gears, shafts, and suspension parts, contributing to the ongoing advancements in automotive technology.Furthermore, the aerospace industry presents another promising market for steel cold forging. As the demand for aircraft continues to soar, the need for high-strength and lightweight components becomes increasingly critical. {Company Name} is well-positioned to meet the stringent requirements of the aerospace sector, providing precision-forged parts that comply with the industry’s rigorous standards for safety and performance.In conclusion, steel cold forging has become an indispensable manufacturing process that offers numerous benefits to industries seeking high-strength, complex components. With its advanced capabilities and commitment to excellence, {Company Name} has established itself as a trusted partner for companies looking to leverage the advantages of cold forging in their product development. As the demand for precision-engineered parts continues to grow, {Company Name} remains at the forefront of delivering innovative solutions that meet the evolving needs of the manufacturing industry.
High-Quality Steel Forged Parts: The Ultimate Guide
Steel Forged Parts, a leading manufacturer of high-quality forged steel parts, has announced the introduction of a new line of products that are set to revolutionize the industry. With a commitment to providing superior quality and innovative solutions, Steel Forged Parts continues to be a driving force in the market.Established in {year}, Steel Forged Parts has built a strong reputation for delivering excellence in every aspect of its business. The company's state-of-the-art manufacturing facilities and cutting-edge technology allow it to produce forged steel parts that meet the highest industry standards. From automotive to aerospace, oil and gas to construction, Steel Forged Parts has a wide range of applications and serves a diverse clientele.The newly launched line of products from Steel Forged Parts demonstrates the company's ongoing dedication to pushing the boundaries of what is possible in the field of forged steel parts. With a focus on innovation and continuous improvement, Steel Forged Parts has developed a series of components that are not only of the highest quality, but also offer unique features and benefits that set them apart from the competition.One of the key highlights of the new product line is the introduction of {specific product}. This groundbreaking component is designed to deliver exceptional performance in even the most demanding applications. Its advanced design and superior material properties make it an ideal choice for industries where reliability and durability are of the utmost importance.In addition to {specific product}, Steel Forged Parts has also expanded its range to include {other specific products}. These new additions further showcase the company's commitment to meeting the evolving needs of its customers and providing solutions that surpass expectations.With a focus on precision engineering and advanced metallurgy, Steel Forged Parts continues to be a trailblazer in the industry. The company's team of skilled engineers and metallurgists work tirelessly to develop and produce forged steel parts that not only meet industry standards but exceed them. This dedication to quality and innovation has earned Steel Forged Parts a loyal customer base and a reputation for excellence.Furthermore, as part of its commitment to sustainability and responsible manufacturing, Steel Forged Parts has implemented environmentally friendly practices throughout its operations. The company's dedication to reducing its environmental impact while maintaining the highest standards of quality is a testament to its forward-thinking approach.In light of the launch of the new product line, {Add Company's Spokesperson name}, {title} of Steel Forged Parts, expressed his enthusiasm for the future of the company. "We are proud to unveil our latest innovations in forged steel parts. Our team has worked tirelessly to develop products that not only meet the needs of our customers but also set new standards for the industry. We are confident that these new additions will further cement our position as a leader in the market."With a commitment to excellence, innovation, and customer satisfaction, Steel Forged Parts continues to be a driving force in the industry. The company's new line of products further demonstrates its dedication to pushing the boundaries of what is possible in the field of forged steel parts. As Steel Forged Parts looks to the future, it is clear that the company will continue to lead the way with its unwavering commitment to quality and innovation.
Ultimate Guide to Sand Casting: Everything You Need to Know
Sand Casting is a widely used method for producing metal parts. It involves pouring molten metal into a sand mold, which is then allowed to cool and solidify, creating the desired shape. This process is particularly well-suited for large and heavy metal parts, as well as complex and intricate designs.One company that specializes in sand casting is {}. With over 30 years of experience in the industry, {} has established itself as a leader in the field of metal casting. The company's state-of-the-art facilities and highly skilled workforce enable it to produce high-quality sand castings for a wide range of industries, including automotive, aerospace, and machinery manufacturing.The sand casting process begins with the creation of a mold made from specially formulated sand. The mold is formed by compacting the sand around a pattern, which is then removed to leave a cavity in the shape of the desired part. Molten metal is then poured into the mold, filling the cavity and taking on its shape as it cools and solidifies. Once the metal has cooled, the sand mold is broken away to reveal the finished casting.{}'s sand casting capabilities are extensive, allowing the company to produce parts in a variety of metals, including aluminum, iron, and steel. This versatility makes sand casting an attractive option for a wide range of applications, from small and intricate components to large and heavy-duty parts. In addition, the company's advanced equipment and technology ensure that each casting meets the highest standards of quality and accuracy.One of the main advantages of sand casting is its ability to produce complex and detailed parts with relatively low tooling costs. This makes it an economical choice for small to medium production runs, as well as for prototype and custom parts. At the same time, the versatility of sand casting allows for the production of large and heavy parts that would be impractical or cost-prohibitive to produce using other methods.In addition to its technical capabilities, {}'s commitment to quality and customer satisfaction sets it apart in the industry. The company's stringent quality control measures ensure that each casting meets the required specifications and standards, while its dedicated team of engineers and technicians work closely with clients to understand their needs and deliver custom solutions. This collaborative approach, combined with the company's expertise and capabilities, has earned {} a reputation for excellence and reliability in the field of sand casting.Looking ahead, {} continues to invest in its facilities and technology to further enhance its sand casting capabilities. The company's ongoing commitment to innovation and improvement ensures that it remains at the forefront of the industry, delivering top-quality castings that meet the evolving needs of its customers.In conclusion, sand casting is a versatile and cost-effective method for producing metal parts, and {}'s expertise and capabilities in this area make it a trusted partner for a wide range of industries. With its advanced facilities, skilled workforce, and dedication to quality, the company is well-positioned to continue meeting the diverse casting needs of its customers for years to come.
The Complete Guide to Die Casting Process and Its Applications
The die casting process is a highly efficient and cost-effective way to produce a wide range of metal parts and components. This manufacturing technique involves injecting molten metal into a steel mold, or die, in order to create complex shapes with a high degree of accuracy and detail. The die casting process is widely used in industries such as automotive, aerospace, and electronics, and it is the preferred method for producing large quantities of metal parts with consistent quality.One company that is a leader in the die casting industry is {}. With over 30 years of experience, {} has established itself as a trusted supplier of high-quality die cast parts and components. The company specializes in producing aluminum, zinc, and magnesium die castings, and their state-of-the-art facilities are equipped with the latest technology to ensure precise and efficient manufacturing processes.{} has a team of skilled engineers and technicians who are dedicated to delivering top-notch die casting solutions to their customers. They work closely with clients to understand their specific requirements and provide tailored manufacturing solutions to meet their needs. This customer-centric approach has earned {} a reputation for excellence in the industry, and they are known for their commitment to quality, reliability, and innovation.In addition to their die casting capabilities, {} also offers a range of value-added services to support their customers throughout the production process. From design and prototyping to machining and finishing, {} provides comprehensive solutions to help clients bring their ideas to life. Their expertise in metal casting and finishing processes allows them to deliver finished parts that meet the highest standards of quality and performance.The company's commitment to sustainability and environmentally friendly practices sets them apart in the industry. {} is dedicated to reducing their environmental impact through efficient production processes and responsible waste management. They also work with sustainable materials and strive to minimize energy consumption in their operations, making them a preferred partner for clients who prioritize environmental stewardship.As a forward-thinking and innovative company, {} is constantly investing in research and development to stay ahead of the curve in the die casting industry. They are always exploring new technologies and techniques to improve their manufacturing processes and deliver even greater value to their customers. By staying at the forefront of advancements in die casting, {} has positioned itself as a leader in the industry and a trusted partner for companies seeking high-quality metal parts and components.In conclusion, the die casting process is a crucial manufacturing technique for producing high-quality metal parts and components. Companies like {} play a vital role in delivering reliable and cost-effective die casting solutions to a wide range of industries. With their expertise, commitment to quality, and dedication to innovation, {} is a leading force in the die casting industry, and they continue to set the standard for excellence in metal manufacturing.
High-Quality Precision Aluminum Casting for Your Needs
Precision Aluminum Casting, a leading manufacturer in the aluminum casting industry, has been providing high-quality precision aluminum castings for over 20 years. The company has established a strong reputation for its dedication to quality, precision, and customer satisfaction.With state-of-the-art facilities and a team of experienced engineers and technicians, Precision Aluminum Casting is capable of delivering a wide range of aluminum casting solutions to meet the needs of various industries, including aerospace, automotive, marine, and more. The company's commitment to innovation and continuous improvement has enabled them to stay ahead of the competition and provide cutting-edge solutions to their customers.Precision Aluminum Casting's expertise in aluminum casting includes the use of advanced technologies such as computer-aided design (CAD) and computer-aided manufacturing (CAM) to ensure precise and efficient production processes. This allows the company to deliver complex and intricate aluminum castings with tight tolerances and high-quality surface finishes.In addition to their technical capabilities, Precision Aluminum Casting places a strong emphasis on quality control and assurance. The company's quality management system is certified to ISO 9001 standards, ensuring that all their products meet the highest quality standards and customer requirements.Furthermore, Precision Aluminum Casting is committed to sustainability and environmental responsibility. The company utilizes eco-friendly practices in their production processes, including the use of recycled aluminum and energy-efficient manufacturing techniques to minimize their environmental impact.The company's dedication to excellence and customer satisfaction has earned them a loyal customer base and a strong reputation in the industry. Their ability to deliver precision aluminum castings with exceptional quality and reliability has set them apart as a trusted partner for many major companies across different sectors.In a recent development, Precision Aluminum Casting has announced the introduction of a new aluminum casting technology that promises to revolutionize the industry. The new technology, which has been in the works for several years, is said to enhance the company's capabilities and enable them to produce even more complex and high-quality aluminum castings."We are excited to introduce this new technology to our production process," said the CEO of Precision Aluminum Casting. "We believe that it will not only improve our efficiency and productivity but also open up new possibilities for our customers in terms of design complexity and performance."The company's investment in new technology demonstrates their ongoing commitment to innovation and staying at the forefront of the industry. The introduction of this new technology is expected to further solidify Precision Aluminum Casting's position as a leader in the aluminum casting market and reinforce their ability to meet the evolving needs of their customers.As Precision Aluminum Casting continues to push the boundaries of what is possible in aluminum casting, they remain dedicated to maintaining the highest standards of quality, precision, and customer satisfaction. With their advanced capabilities and commitment to excellence, the company is well-positioned to continue delivering cutting-edge solutions to their customers for many years to come.
High-quality custom aluminum cylinders in China: Discover the best options for your needs
China Custom Aluminum Cylinder Company Introduces Innovative New Product Line China Custom Aluminum Cylinder Company is proud to announce the launch of their latest product line – custom aluminum cylinders. With years of experience in the industry, the company has established itself as a leader in providing high-quality, reliable, and efficient aluminum cylinders for a wide range of applications.The new custom aluminum cylinders are designed to meet the specific needs of their customers, offering a customizable solution for a variety of industrial and commercial purposes. The company’s state-of-the-art manufacturing facilities and advanced technology allow them to produce cylinders that are precisely tailored to their customers’ requirements, ensuring optimal performance and durability.One of the key features of the custom aluminum cylinders is their lightweight yet durable construction, making them ideal for use in a wide range of applications. Whether it be in the automotive, aerospace, or manufacturing industries, these cylinders offer a versatile and efficient solution for powering various mechanical systems.In addition to their superior quality, the custom aluminum cylinders also boast a high level of corrosion resistance, ensuring longevity and reliability even in the most demanding environments. This makes them an ideal choice for customers looking for a cost-effective and low-maintenance solution for their cylinder needs.The company’s commitment to quality and innovation is further demonstrated by their strict adherence to international standards and stringent quality control processes. Each custom aluminum cylinder undergoes rigorous testing to ensure it meets the highest industry standards, giving customers peace of mind knowing they are investing in a superior product.Furthermore, China Custom Aluminum Cylinder Company prides itself on its dedication to customer satisfaction and service. Their team of highly skilled engineers and technical experts work closely with customers to understand their specific requirements and provide tailored solutions that meet their unique needs.To complement their product line, the company also offers comprehensive technical support and after-sales service, ensuring that customers have access to the expertise and assistance they need throughout the lifecycle of their custom aluminum cylinders.With the launch of their new custom aluminum cylinder product line, China Custom Aluminum Cylinder Company is poised to further solidify their position as a leading provider of high-quality aluminum cylinders in the global market. Their dedication to excellence, innovation, and customer satisfaction sets them apart from their competitors and makes them the go-to choice for businesses looking for reliable and efficient cylinder solutions.In conclusion, the introduction of the custom aluminum cylinder product line by China Custom Aluminum Cylinder Company represents a significant milestone in the company’s continued commitment to excellence and innovation. Their dedication to quality, customization, and customer satisfaction sets them apart as a leader in the industry, and their new product line is sure to make a positive impact in the market. For businesses looking for high-quality, reliable, and efficient aluminum cylinders, China Custom Aluminum Cylinder Company is undoubtedly the provider of choice.
High-Quality Steel Die Forging: What You Need to Know
Steel Die Forging Technology Advancing with the Company's ExpertiseSteel die forging is a critical process that is used to create high-quality components with superior strength and durability. One company that has been leading the way in this industry is {}, which has been a trusted provider of steel die forging solutions for over 20 years. As a leading expert in the field, {} is constantly advancing its technology and capabilities to meet the evolving needs of its customers.Steel die forging is a manufacturing process that involves shaping and forming metal using a set of dies under high pressure. This process allows for the creation of components with a high degree of precision and strength, making it an essential technique in industries such as automotive, aerospace, and defense. {} has established itself as a key player in this field by offering a wide range of forging capabilities, including open-die forging, closed-die forging, and seamless rolled ring forging.One of the key factors that sets {} apart from its competitors is its commitment to investing in state-of-the-art technology and equipment. The company has a modern manufacturing facility that is equipped with advanced machinery, including hydraulic presses, forging hammers, and heat treatment furnaces. This allows {} to produce high-quality forgings with tight tolerances and exceptional mechanical properties.In addition to its impressive technology, {} also takes pride in its team of experienced engineers and metallurgists who possess a deep understanding of the forging process and materials. This expertise allows the company to provide valuable insights and recommendations to its customers, helping them optimize their designs for improved manufacturability and cost efficiency.One of the most recent advancements at {} is the implementation of computer-aided design (CAD) and computer-aided manufacturing (CAM) software, which has further enhanced the company's capabilities in producing complex forgings with intricate geometries. This investment in digital technology has significantly shortened lead times and improved overall efficiency in the production process.Furthermore, {} places a strong emphasis on quality control and assurance, with a dedicated team that rigorously inspects and tests every forging to ensure it meets the highest industry standards. The company is certified to ISO 9001 and AS9100 standards, demonstrating its commitment to delivering forgings that consistently meet or exceed customer expectations.With a focus on continuous improvement, {} is also exploring new opportunities in research and development to expand its capabilities and explore new markets. The company is actively collaborating with its customers to develop innovative solutions for challenging applications, further solidifying its position as a trusted partner in the steel die forging industry.In conclusion, the steel die forging capabilities offered by {} are unparalleled in terms of quality, precision, and reliability. With a combination of advanced technology, experienced professionals, and a dedication to innovation, the company continues to set the standard for excellence in the forging industry. As the demand for high-performance components continues to grow, {} is well-positioned to meet the needs of its customers and drive the industry forward with its cutting-edge solutions.
Quality Hot Forging Parts Factories: Reliable and Efficient Manufacture
Hot Forging Parts Factory Expands Production Capability to Meet Growing DemandWith the continuous development of the automobile and machinery manufacturing industry, the demand for hot forging parts is on the rise. In response to this growing demand, the hot forging parts factory of {} has expanded its production capability to meet the needs of its customers.Established in 1998, {} is a leading manufacturer of hot forging parts for various industries, including automotive, machinery, and aerospace. The company has a strong focus on quality and innovation, and its hot forging parts are known for their high precision and durability.In order to keep up with the increasing demand for its products, {} has recently made significant investments in its production facilities. The factory has been equipped with state-of-the-art forging equipment, including high-speed forging presses and advanced heat treatment systems. This expansion has allowed the company to increase its production capacity and shorten lead times, ensuring that it can deliver its products to customers in a timely manner.Furthermore, {} has also invested in the latest technology for quality control and testing. The company has implemented a stringent quality assurance system to ensure that every hot forging part meets the highest standards of precision and durability. This commitment to quality has earned {} a strong reputation in the industry, and the company's products are highly regarded by its customers.In addition to its investments in production technology, {} has also focused on developing its workforce. The company has provided comprehensive training programs for its employees to ensure that they have the skills and knowledge necessary to produce high-quality hot forging parts. This focus on human capital development has helped {} to build a team of highly skilled and dedicated professionals who are committed to delivering excellence in every aspect of their work.The expansion of {}'s hot forging parts factory is expected to have a significant impact on the company's business. With its increased production capacity and improved capabilities, {} is well-positioned to take advantage of the growing demand for hot forging parts in the market. The company is confident that it will be able to serve its customers better than ever and continue to be a trusted partner for the automotive, machinery, and aerospace industries.At the same time, {} is also committed to sustainability and environmental responsibility. The company has implemented measures to minimize its environmental impact, including the use of energy-efficient production processes and the recycling of waste materials. By taking these steps, {} is demonstrating its commitment to being a responsible corporate citizen and contributing to a healthier planet.Looking ahead, {} is confident that its expanded hot forging parts factory will enable the company to achieve even greater success in the future. With its focus on quality, innovation, and customer satisfaction, {} is well-positioned to continue growing and serving the needs of its customers for many years to come.
High-quality Lost Wax Casting Parts: Everything You Need to Know
(Company Name) is proud to announce the launch of our new line of Lost Wax Casting Parts, which are designed to meet the demanding needs of various industries including aerospace, automotive, and energy. Our Lost Wax Casting Parts offer superior strength, durability, and precision, making them the ideal solution for a wide range of applications.Lost wax casting, also known as investment casting, is a process that has been used for centuries to create intricate and detailed metal parts. This traditional method involves creating a wax model of the desired part, which is then coated with a ceramic material and heated to remove the wax, leaving behind a hollow ceramic mold. Molten metal is then poured into the mold, allowing it to take the exact shape of the original wax model. Once the metal has solidified, the ceramic mold is broken away, leaving behind the finished metal part.Our Lost Wax Casting Parts are crafted using the latest advancements in casting technology, ensuring that each part is produced with the highest level of precision and accuracy. This results in parts that are not only strong and durable, but also free from defects and imperfections. Our dedication to quality and innovation means that our Lost Wax Casting Parts are capable of meeting the most stringent performance requirements, making them a reliable choice for even the most demanding applications.In addition to their exceptional performance characteristics, our Lost Wax Casting Parts are also highly customizable, allowing us to tailor each part to the specific needs of our customers. Whether it's a complex aerospace component or a critical automotive part, we have the expertise and capabilities to deliver Lost Wax Casting Parts that are perfectly suited to the task at hand. Our team of skilled engineers and technicians work closely with our customers to understand their unique requirements, ensuring that every part we produce meets their exact specifications.With the launch of our new line of Lost Wax Casting Parts, we are excited to offer our customers a comprehensive solution for their metal part needs. Our commitment to quality, innovation, and customer satisfaction sets us apart as a leader in the casting industry. We are dedicated to providing our customers with the highest quality parts, backed by exceptional service and support.As a leading manufacturer of precision metal parts, (Company Name) has a long history of delivering innovative solutions to our customers. Our state-of-the-art facilities and advanced manufacturing capabilities allow us to produce a wide range of complex and high-precision parts, serving a diverse range of industries. Our team of experts is committed to pushing the boundaries of what is possible, and our new line of Lost Wax Casting Parts is a testament to that commitment.In conclusion, the launch of our new line of Lost Wax Casting Parts represents a significant milestone for (Company Name) and reinforces our position as a leader in the casting industry. With their superior strength, durability, and precision, our Lost Wax Casting Parts offer a reliable solution for a wide range of applications. We are excited to bring these innovative parts to market and look forward to continuing to serve our customers with the highest quality products and service.
High-Quality Custom Copper Manufacturer for Your Business Needs
Custom Copper Manufacturer Announces Expansion to Meet Growing DemandCustom Copper Manufacturer is pleased to announce the expansion of its production facilities in order to meet the growing demand for its high-quality copper products. The company, which has been in operation for over 20 years, has seen a significant increase in orders for its custom copper parts and components, particularly in the automotive and electronics sectors.The expansion will see Custom Copper Manufacturer increase its production capacity by 30%, allowing the company to fulfill larger orders and reduce lead times for its customers. The company has invested in new state-of-the-art machinery and equipment to streamline its manufacturing processes and ensure that the highest quality standards are maintained.Custom Copper Manufacturer takes great pride in its ability to provide custom copper solutions for a wide range of industries. The company works closely with its customers to understand their specific requirements and develop customized solutions that meet their exact needs. From small, intricate parts to large, complex components, Custom Copper Manufacturer has the expertise and capabilities to handle any project.One of the key factors driving the increased demand for custom copper products is the growing trend towards miniaturization in the electronics industry. As electronic devices become smaller and more sophisticated, the need for precision-engineered copper components has never been greater. Custom Copper Manufacturer has positioned itself as a leader in this space, offering a range of high-precision machining services to meet the exacting requirements of its electronics customers.In addition to the electronics industry, Custom Copper Manufacturer also serves the automotive sector, where copper parts and components are used in a wide range of applications. From electrical wiring and connectors to heat exchangers and radiator cores, copper plays a critical role in the performance and reliability of modern vehicles. With the expansion of its production facilities, Custom Copper Manufacturer is well positioned to meet the growing demand from its automotive customers.The company's commitment to quality is evident in its ISO 9001 certification, which reflects its dedication to upholding the highest standards of manufacturing and quality control. Custom Copper Manufacturer's team of experienced engineers and technicians work tirelessly to ensure that every product that leaves its facility meets the most rigorous quality standards."We are excited to announce the expansion of our production facilities to meet the increasing demand for our custom copper products," said the CEO of Custom Copper Manufacturer. "This expansion represents a significant investment in our future and will allow us to better serve our customers and continue to grow our business."The expansion is expected to create new job opportunities in the local community, providing a welcome boost to the economy. Custom Copper Manufacturer is committed to supporting the local workforce and providing a safe, rewarding work environment for its employees.As the demand for custom copper products continues to rise, Custom Copper Manufacturer is well positioned to meet the needs of its customers and provide them with the high-quality solutions they have come to expect. The company's expansion is a testament to its commitment to excellence and its determination to remain at the forefront of the custom copper manufacturing industry.